
RUBIS: Data-driven development and fabrication of ceramics and thermostructural composites: Research platform on the Factory of the Future, the Big data, the Artificial Intelligence and the associated Information Systems
Coordinator: Fabrice ROSSIGNOL
IRCER – Institut de Recherche sur les CERamiques
(UMR 7315 CNRS/Univ. Limoges)
Keywords: Ceramic and ceramic matrix composite materials, additive manufacturing, factory of the future
RUBIS, Research Platform on the Factory of the Future, Big data, Artificial Intelligence and associated Information Systems, focuses on ceramics and thermostructural composites capable of resisting harsh environments.
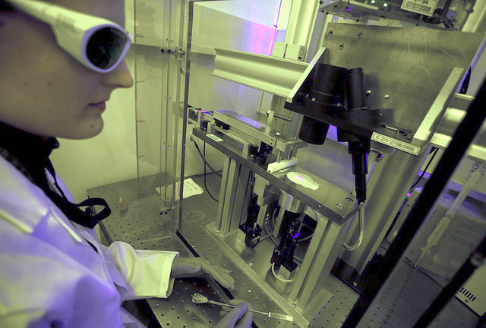
The need for such materials at high temperatures is in fact an urgent necessity in several fields: energy, transport, defense, etc. Their toughness/refractory character allows them to be used in aeronautics, space or nuclear applications for example. The science of these modern materials and associated manufacturing processes requires consideration of a multidisciplinary approach including chemistry, physics and engineering, closely linked to leveraging data science via artificial intelligence (AI) to accelerate the entire manufacturing value chain.
RUBIS covers all design and material processing issues: shaping by additive manufacturing, consolidation post-treatments (for example drying, debinding/pyrolysis, sintering). The RUBIS project aims to transform a set of design and manufacturing tools into an “integrated smart factory” to improve productivity and quality control providing traceability of manufactured parts. With the complete digitalization of all stages, RUBIS also intends to optimize the performance of manufactured parts, reduce their costs as well as energy consumption and environmental impact, and increase the degree of flexibility of production allowing the delivery of products entirely customizable and high quality.
The two RUBIS deliverables planned for year 5 will be two platforms:
- a CAD tool platform for the design of optimized ceramic and composite structures,
- a fully digitalized manufacturing platform integrating the stages of shaping by additive manufacturing and thermal post-consolidation with Machine Learning (ML) capabilities for each of said manufacturing stages.
The 2 associated milestones are planned for year 3 and correspond to the platform specifications. The materials under study will be both oxide and non-oxide materials suitable for the severe environments envisaged. In the particular case of the manufacturing process, oxides such as alumina with well-documented behavior laws in the literature will be used to initiate developments.