Conventional metallurgy
Description
This platform allows the development of model alloys (Fe, Ni, Cr, Co, Al base) of high purity and well-controlled chemical composition. The alloys are melted by induction fusion in a large volume cold boat, thus making it possible to prepare ingots weighing between 300 and 3000 g. The fusion takes place under a controlled atmosphere.
The cast ingots can be wrought by cold rolling (to obtain pieces of sheet metal with a thickness of 2 to 5 mm) or by hot forging (to produce cylindrical bars with a diameter of 12 to 14 mm). Soon (end of 2024), a hot press should complete the grinding equipment.
The main equipment of the platform was financed by the AURA Region (IRICE program) and by the MINES-Télécom Institute. The hot press (currently being acquired) is co-financed by PEPR DIADEM and MINES of St-Etienne.
The technical staff of the platform: 1.5 FTE laboratory technician and 0.5 FTE research engineer (people from MINES St-Etienne).
Location
MINES de St-Etienne, Laboratoire Georges Friedel, UMR CNRS 5307, 158 Cours Fauriel, 42023 St-Etienne.
Contacts
Responsible of the plateform : Anna FRACZKIEWICZ
Associated targeted project coordinator: Alexis DESCHAMPS
Technical characteristics
- Cold nacelle melting furnace, working in a controlled atmosphere. Ingot mass: 300 to 3000 g. Maximum alloy melting temperature: 1800°C.
- Drop hammer allowing hot forging. Maximum mass during a forging operation: 500 g of alloy.
- Heat treatment ovens, maximum T 1200°C.
- Cold rolling mill. Maximum mass of alloy transformed in one operation: approximately 200 g.
- Hot press, maximum temperature: 1100°C. Maximum mass during a working operation: 500 g of alloy.
Associated targeted project
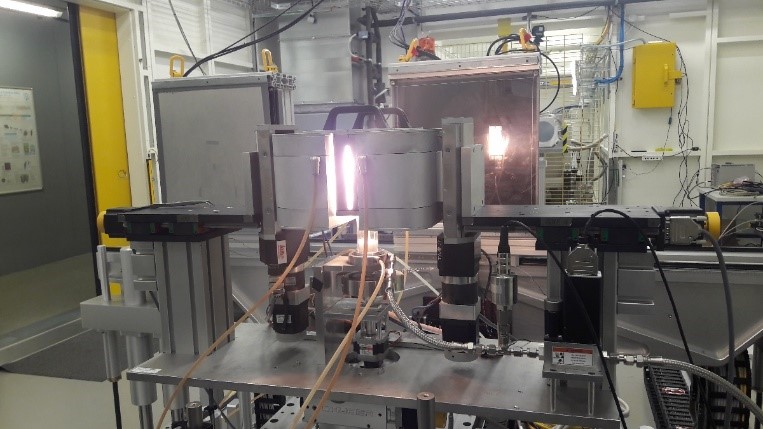