3D Saclay (powder bed, cladding, wire, extrusion)
Description
From the laboratory scale to the pilot project, 3D Saclay develops and optimizes innovative materials with metal and ceramic matrices and ensures the control of their manufacturing, treatment and assembly processes. It is positioned across the entire value chain from formulation, raw material synthesis, powder and wire additive manufacturing, to advanced characterizations, modeling and prenormative research.
Location
CEA Paris-Saclay (460, 467 et 611 buildings).
Contacts
Responsible of the platform: Céline CABET
Associated targeted project coordinator: Alexis DESCHAMPS
Technical characteristics
Synthesis/recycling of the raw material:
- ATO Lab atomizer: 70-200µm powder, O2/N2 control, production 1kg/day.
- TEKNA 30kW plasma torch: 5-200µm powder under Ar/H2 and O2, production 1kg/h.
Consolidation :
- Milling: CM01 and CM20 ZOZ attritors from 200g to 2kg + knife/ball/vibration mills + BAG.
- Electric arc melting furnaces (including refractory metals) + spinning press, drawing bench with hydraulic cylinder, wire drawing machine.
Additive manufacturing:
- Laser powder bed fusion: 2 SLM Solutions 280 (upgraded 280HL and Production series), 2 Trumpf TruPrint 1000.
- Laser cladding: OPTOMEC MTS-CA + 3kW IPG laser and MELTIO (Wire/powder) + 6 200W DLs.
- WAAM cell: with MIG-MAG-CMT, TIG and Fronius plasma generator, wire preheating system, two-wire configuration.
- WLAM cell with inerting and cooling plate (maximum size 1000x800x500mm3).
- Ceramic 3D printing: Fused deposition Modeling (FDM) process.
Processing/finishing:
- Heat treatments.
- Surface treatments.
Supports: Means of mechanical and microstructural characterization, Means of advanced characterization, modeling/simulation, standards
Associated targeted project
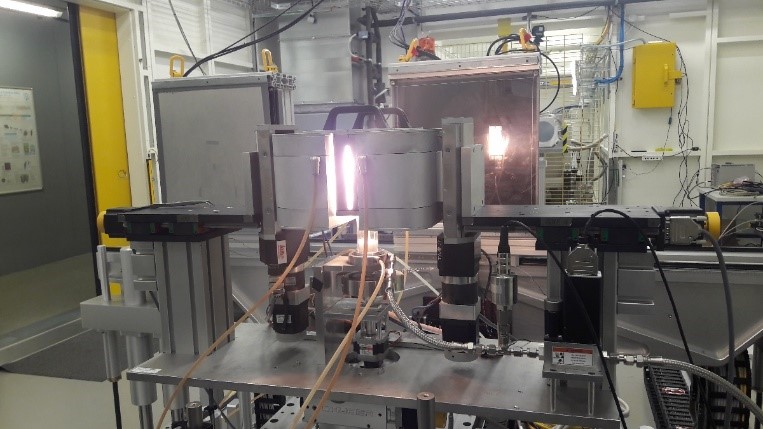