1600°C so-called pixelated sintering oven
Description
Pixelated sintering relies on fine and localized control of heat input. The heating elements are arranged around the part to be sintered based on upstream multi-physics modeling. The basic unit consists of a power supply, a resistive heating element, and a thermocouple placed as close as possible to the sample. This unit can be repeated “infinitely” (i.e. discretization of the heating system, pixelated oven). The entire sintering cycle is controlled by proprietary software (GALTENCO Solutions Company) which controls each heating resistor independently, thanks to the thermocouple matched to it. The energy delivered to the room is optimized and thermal losses limited. Beyond energy intensification, sintering is free, which opens perspectives for the consolidation of complex 3D parts and the transfer of scale to large dimensions. Real-time control of part removal makes it possible to optimize the sintering cycle via AI.
Location
IRCER, Limoges.
Contacts
Platform manager / Coordinator of the associated targeted project: Fabrice ROSSIGNOL
Technical characteristics
Technical characteristics (currently being consolidated with the GALTENCO Company on the instrumentation part because this type of device is entirely new).
- Useful area: 20*20*40 cm.
- Max temperature: 1600°C.
- 30 SiC resistors.
- WIFI temperature measurement.
- 3 windows for instrumentation.
Associated targeted project
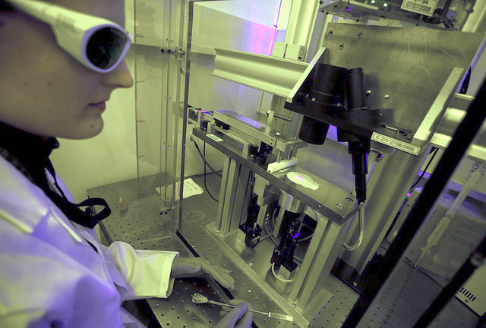